
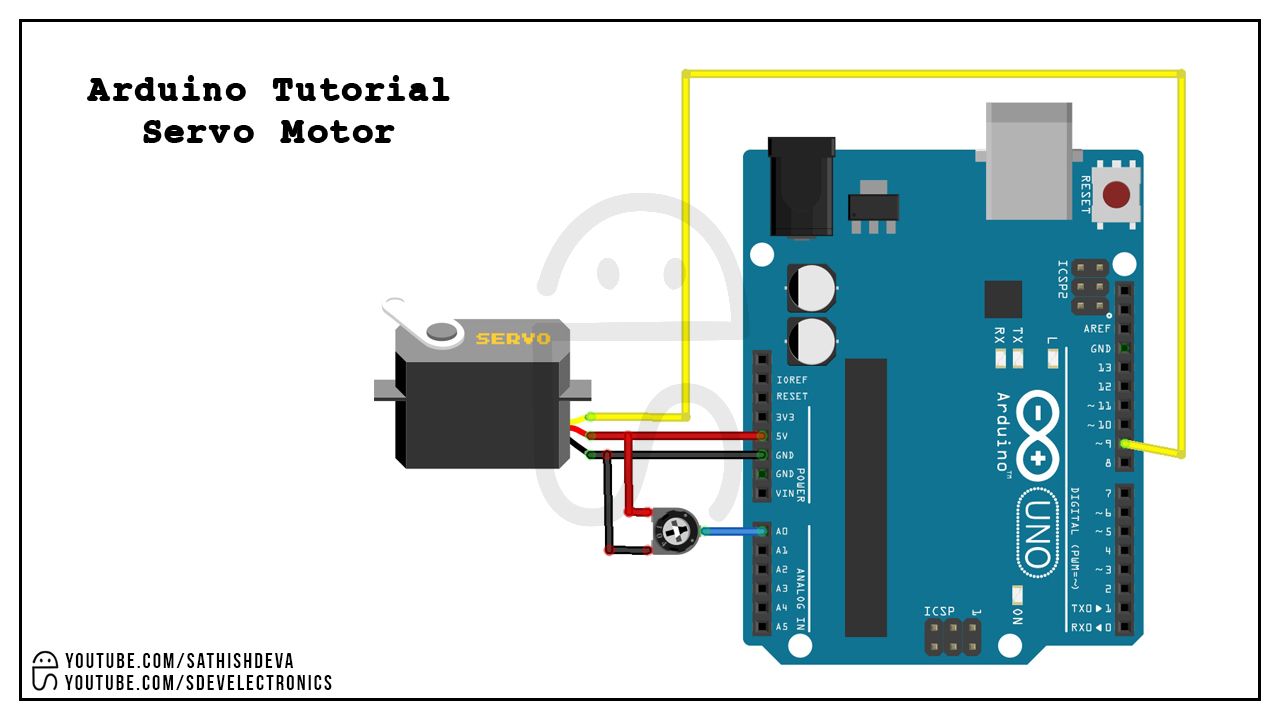
Panduit’s M12 cordsets are rated for ten million flex cycles, providing durability and reliability.Ĭost-effective and reliable - ideal for commercial and industrial applications with limited space. IndustrialNet™ M12 Cat 5e and Cat 6A Overmolded Cordsets Solutions for 5G, smart home, industrial, automotive, healthcare, and agricultural IoT applications. Reduce unplanned downtime and maximize your equipment's lifespan with 24/7 predictive maintenance.Īt the Forefront of Enabling IoT Applications Würth Elektronik WE-STAR-TEC Cable Ferrites with Safety Key Technology
SERVO MOTOR ARDUINO UNO SERIES
WR-FFC Series Pre-Folded Flat Flexible Cable
SERVO MOTOR ARDUINO UNO SOFTWARE
The STM32Cube with graphical software configuration tool reduces development efforts, time, and cost TRACO Power’s TMW Series 24 W and 36 W AC/DC power supplies are IP68 rated and fully encapsulated.
SERVO MOTOR ARDUINO UNO CODE
The Arduino Servo Motor control tutorial is explained in step by step of C code given below.Ģ4 W and 36 W AC/DC Industrial and Medical Power Supplies – TMW Series To do this we have “Sg90.attach(3) ”, here we are telling the UNO we connected the signal pin of servo at PIN3.Īll left is to set the position, we are going set the position of servo by using “Sg90.write(30) ”, by this command the servo hand moves 30 degrees, so that’s it. After that whenever we need to change the position of servo we need to call the command ”Sg90.write(needed_position_ angle) ”. In this circuit we will have two buttons one button increases the position of servo and the other is for decreasing the position of servo. Now we tell the UNO where the signal pin of servo is connected or where it needs to generate the PWM signal. Now we need to define a name for the servo “Servo sg90sevo”, here ‘sg90servo’ is the name chosen, so while writing for potion we are going to use this name, this feature comes in handy when we have many servos to control, we can control as many as eight servo by this.
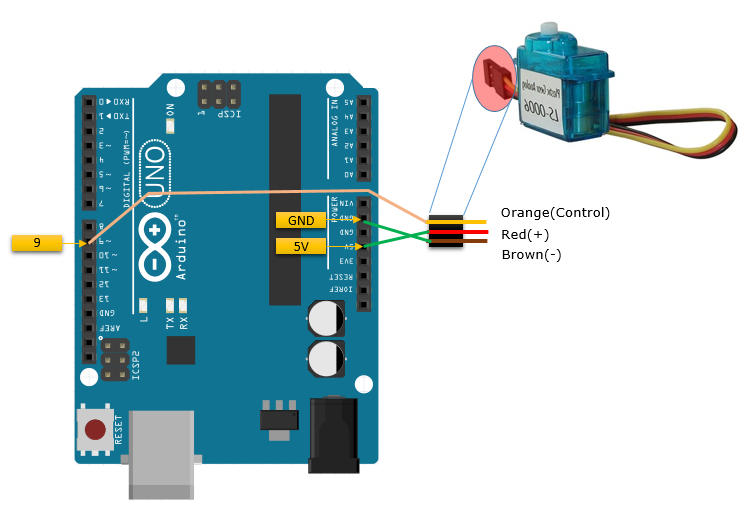
The important thing here is the DUTY RATIO of the PWM signal. The frequency of PWM (Pulse Width Modulated) signal can vary based on type of servo motor.

This data regarding position of shaft is sent through the SIGNAL pin. The position data to the control should be sent in the form of PWM signal through the Signal pin of servo motor. Simply speaking the control electronics adjust shaft position by controlling DC motor. The RED wire is connected to power, Black wire is connected to ground and YELLOW wire is connected to signal.Ī servo motor is a combination of DC motor, position control system, gears. The position of the shaft of the DC motor is adjusted by the control electronics in the servo, based on the duty ratio of the PWM signal the SIGNAL pin. A servo motor will have mainly there wires, one is for positive voltage another is for ground and last one is for position setting. Servo motors are available at different shapes and sizes. These motors are used in robotic arm machines, flight controls and control systems. These are proposed for low speed, medium torque and accurate position application. These are not proposed for high speed applications.
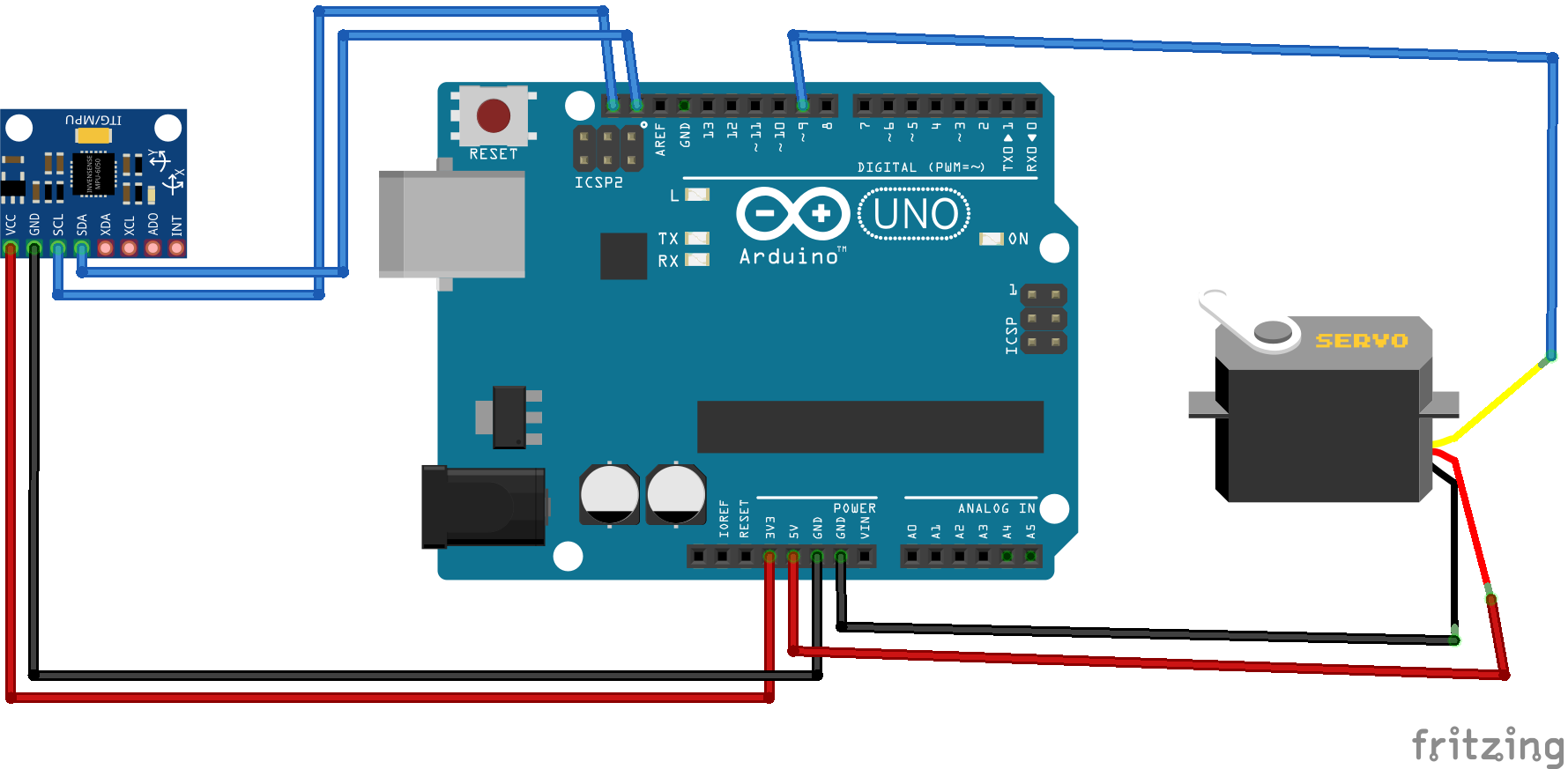
Servo Motors are used where there is a need for accurate shaft movement or position. In this tutorial we are going to control a servo motor by ARDUINO UNO.
